Week 7: Propellers and Servos
April 18, 2024
Welcome back to your weekly installment of delivery drone development! Last week, I got my drone (her name is Boomerang) to hit the skies with pure finesse.
Now with Boomerang ready to fly, I set her to the side and began focusing on other aspects of the drone delivery process. An essential point of innovation on drones is the propeller systems. We’re so used to seeing traditional dual blade setups on drones, but there’s a whole realm to discover. Drone propellers can affect thrust, RPM, battery life, and sound.
I wanted to specifically focus on sound. You see, I’d hate for a bunch of drones to be flying around my neighborhood creating obnoxious, high-pitched noises while I’m trying to focus on watching The Office. So, I did a deep dive into propeller designs and landed upon the toroidal propeller. It’s been used on boats for a while (see Sharrow Marine propellers), but researchers at MIT’s Lincoln Laboratories have fitted toroidal propellers onto drones. What they found is that they are far more noise efficient than traditional dual bladed propellers.
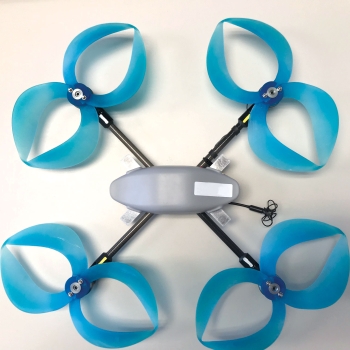
I got in touch with Dr. Thomas Sebastian from MIT Lincoln Laboratories who did extensive work with toroidal propellers. Using his research and advice, I 3D printed rough prototypes of the toroidal prop design and attached it to a 920 KV motor to test its noise and thrust efficiency compared to other propellers.
The experimental setup consisted of the following parts:
- Digital load cell (1 kg) + HX711 board 3D printed test stand
- Arduino Uno
- Phone with Decibel Meter app
- 920 KV Motor
- 3D printed propellers (pictures displayed in following pages) of equivalent diameter (~10cm)
- Propellers: Standard 2 blade, Standard 3 blade, Toroidal 2 blade, Toroidal 3 blade
- Electronic Speed Controller
- 11.1V LiPo battery
- Servo tester
- Neiko digital handheld tachometer
- Laptop to run thrust/load application
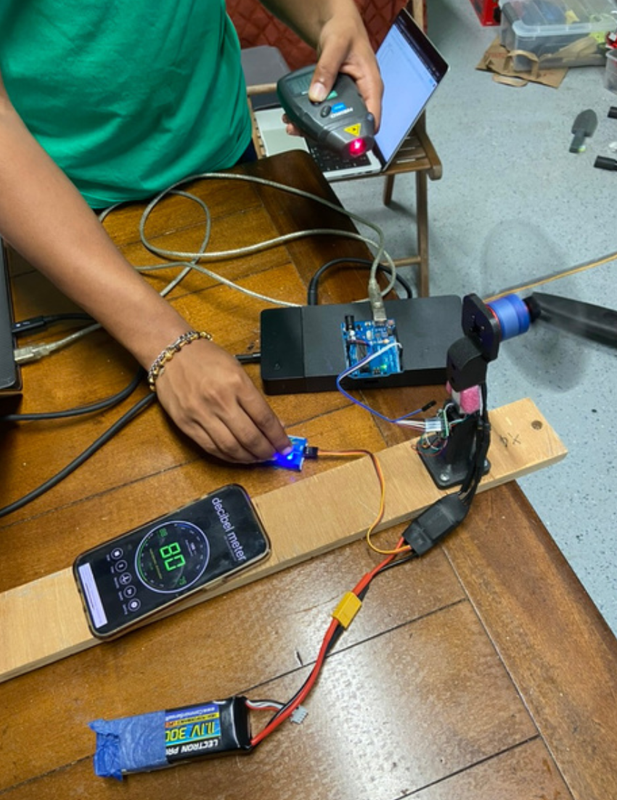
To obtain data for each of the props, I set up a spreadsheet to take measurements of RPM, thrust (kg), and decibels . As shown in the images, I initially positioned the phone behind the stand by 15 cm, but later I shifted it 24.5 cm to the left of the stand because the decibel readings fluctuated more due to vortex development in that region. This provided far more precise decibel readings.
I took data for thrust and noise at 1000 RPM increments from 3000 RPM to 10000 RPM. Then, I plotted RPM vs. Thrust to measure lift efficiency and Thrust vs Decibels to measure noise efficiency.
From my tests, it was clear that the toroidal 3 blade propeller was the winner in terms of thrust and noise efficiency. At 10,000 RPM, the toroidal propeller produced 0.18 kilograms of lift as compared to the 3 blade propeller that only produces 0.09 kilograms of lift at the same RPM.
Additionally, when analyzing the emitted sound at 0.04 kilograms of thrust, the toroidal propeller emits the lowest intensity at about 68 decibels compared to the runner-up: the 3 blade standard propeller at 75 decibels.
Because of the cantilevered structure of conventional propellers, they are susceptible to deformations that increase noise through further wind resistance. On the other hand, the toroidal propeller design has a closed loop structure that reduces vibration and dissipates noise. This explains the toroidal 3 blade propeller’s superior performance.
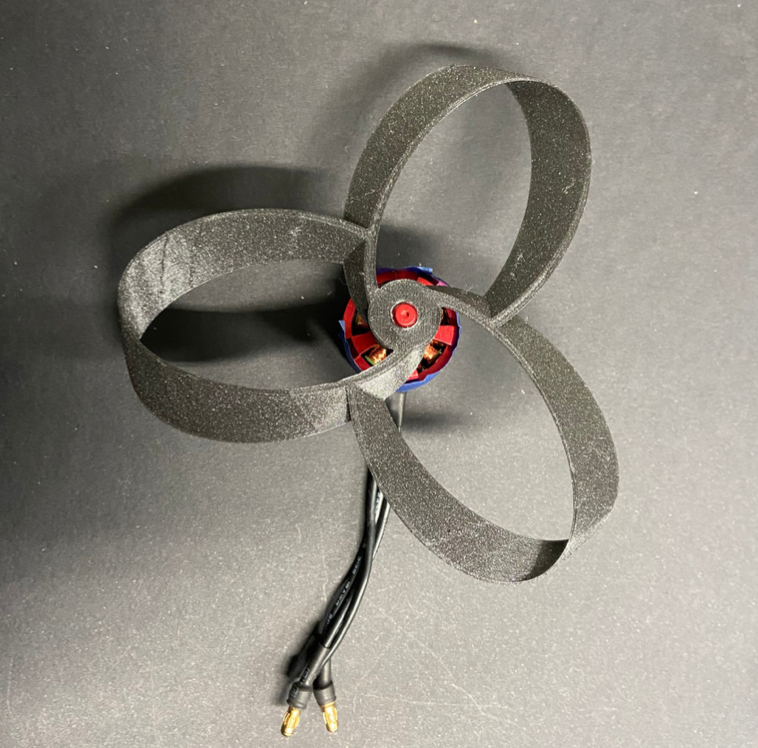
Throughout this test, there are many possible sources of error. Most notably, slight differences in propeller diameter can contribute to errors in thrust and noise efficiency. A larger propeller diameter will increase both the thrust and sound intensity because it is pushing larger volumes of air.
Propeller pitch angle is also an essential variable to consider. On airplanes, there are systems in place to adjust pitch angles. For example, lower pitch angles make the engine reach its maximum RPM at lower lower speeds. On large delivery drones like the ones I plan to build, the variable-pitch adjustment mechanism I developed in the first few weeks of this project may help with range and noise efficiency.
I’m uncertain if I’ll be able to mount the toroidal 3-blade propellers onto Boomerang because 3D printed propellers aren’t the most reliable. They crack easily, they’re uneven, and they’re heavy. However, this experiment proves that the toroidal design will be an effective solution for noisy drone propellers. The next challenge to solve would be molding and manufacturing properly designed toroidal propellers for real-world applications.
Leave a Reply
You must be logged in to post a comment.