03: The Recycling Process of Lithium-Ion Batteries
March 15, 2024
Hi everyone! In this post, I will discuss the importance of battery recycling and the lithium-ion battery recycling process.
Circular Economy
When talking about recycling (in general), you might see the phrase “circular economy” come up a lot (or at least I did in my research).
A circular economy is an economic system designed to minimize waste and make the most of resources by reusing, repairing, or recycling materials and products, rather than being disposed of after use. This approach aims to create a closed-loop system where resources are continuously circulated within the economy, reducing the need for new resource extraction and minimizing environmental impact.
Some materials that exist in such a circular economy include glass, paper/card, steel, aluminum, plastic bottles, car catalysts and lead acid batteries. These are all well established and mature markets which grow at a manageable rate.
However, when new disruptive products and innovations come to the market with large growth potential, a product can rapidly become an environmental issue if a circular economy has not been designed with the product. Examples include the rapid growth of PET bottles, the rapid growth of waste electrical and electronic equipment (WEEE) or the rapid demise of cathode ray tubes.
Disruptive growth in technologies can occur when a new product becomes easy to mass produce, bringing it within the reach of a larger potential market. In the case of batteries, a key disruption was environmental regulation and focus on renewable energy, which has led to a shift from internal combustion engine to electric vehicles and an increase in the demand for metals such as Co, Ni, Li and Nd.
Recycling a Li-Ion Battery
Note: Battery recycling methods vary depending on the type of battery, so the following steps are specific to LIBs.
Before a battery is sent to a recycling facility, it is first evaluated for reuse—either being put back into a device similar to their original one or being repurposed in a different type of product or application. In the end, reuse simply delays the inevitable recycling of batteries when it finally hits the end of its life.
First, batteries go through pretreatment processes to separate the battery elements and prepare the valuable components for further processing. It consists of 3 main stages: discharge, dismantling, and separation.
A battery first needs to be discharged of any remaining power to prevent short circuits. There are many methods to do this; the most common is to use a salt solution, such as sodium sulfate (Na2SO4) or sodium chloride (NaCl). After discharging, the battery is disassembled and and separated into the categories: cathode, anode, and organic diaphragm. While this step can be done by hand; for mass amounts of batteries, machines do most of the work through shredding, sieving, magnetic classification, and segregation. Finally, the separation stage can consist of physical (such as floatation), mechanical (such as shredding and crushing), thermal (such as organic components evaporation), chemical (such as dissolution of binder or foils), and mechano-chemical processes.
After these steps, there remain:
“Black mass” (a granular material made up of the shredded cathodes and anodes of the batteries)
Copper and aluminum foils (which held the anode and cathode material)
Separators (thin plastic films)
Other plastics
Steel canisters
Electrolyte
Black mass contains the materials that can be further processed and made into new battery cathodes and anodes.
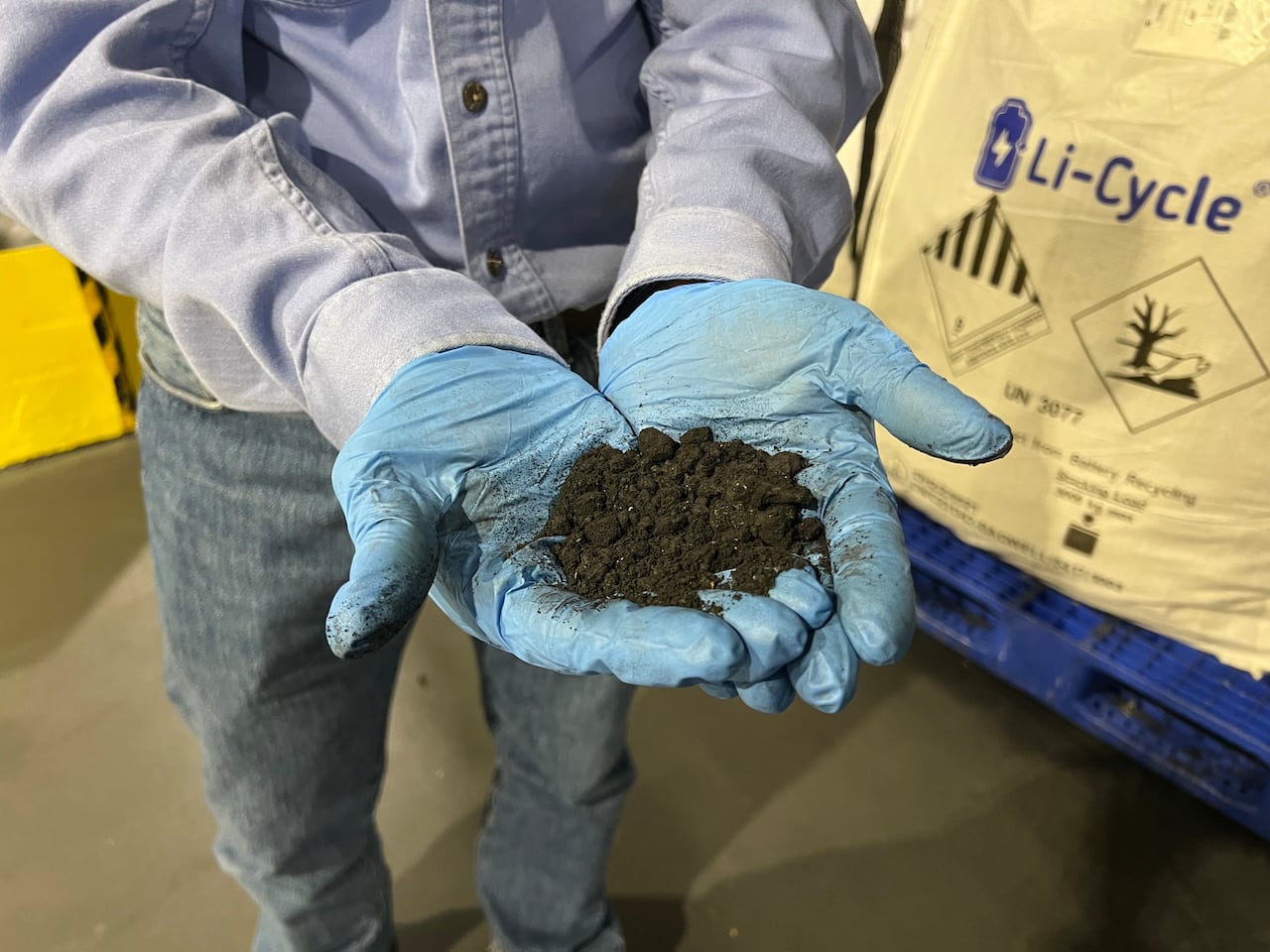
Recovering Black Mass
To recover black mass, there are currently 2 main methods: pyrometallurgy and hydrometallurgy.
Pyrometallurgy uses heat, such as through smelting or roasting, to convert the metal oxides used in battery materials to either metals or metal compounds. It consists of thermal reduction, smelting, and salt roasting. It results in elemental ‘building blocks’ that can be used to make new cathodic substances. Pyrometallurgy is often used due to its rapidity, simplicity, and flexibility. However, this method also requires large amounts of energy and releases toxic gases (such as CO2). This method also results in low product purity and only recovers copper of the foil and nickel and cobalt from positive electrodes, and not other materials like plastics, graphite, and aluminum.
Hydrometallurgy uses aqueous solutions to dissolve and extract metals from battery resources. It consists of leaching and recovering high-value elements from the leachate. The leachant usually consists of inorganic acids such as nitric acid (HNO3), phosphoric acid (H3PO4), hydrochloric acid (HCl), and sulfuric acid (H2SO4). Elements in the leachate are then extracted through separation and purification methods such as solvent extraction, electrolysis, and precipitation. Compared to pyrometallurgy, hydrometallurgy generates less emissions and needs less energy. It also recovers the metals individually, as opposed to the pyrometallurgical process, where metals are recovered as alloys. However, this method requires first sorting, which increases cost and complexity. It also releases unwanted wastewater.
Finally, there is also a third battery recycling method currently in development: direct recycling, which saves energy by skipping the shredding step and preserves the highly engineered cathode structure. However, one of the main obstacles that this method currently faces is the multiple material inputs, which can result in a lower efficiency and purity of the recycled batteries. Direct recycling is also relatively new, so it is currently only seen at the laboratory level and has yet to be tested and used by the industry.
Thus, there really is no ‘perfect’ way to recycle batteries, as they each have their drawbacks.
Sources
Dobó, Z.; Dinh, T.; Kulcsár, T. A review on recycling of spent lithium-ion batteries. Energy Reports 2023, 9, 6362–6395. https://doi.org/10.1016/j.egyr.2023.05.264.
Zanoletti, A.; Carena, E.; Ferrara, C.; Bontempi, E. A review of Lithium-Ion battery recycling: Technologies, sustainability, and open Issues. Batteries 2024, 10 (1), 38. https://doi.org/10.3390/batteries10010038.
Leave a Reply
You must be logged in to post a comment.